In recent decades, US and EU markets have outsourced a lot of their production to lower cost centres in Asia. Now with the rampant rise in transportation costs (up approximately 500% in the US from a year ago[1]) and energy costs (oil prices are up by more than 65% since January[2] ), the entire supply chain is affected globally. Supply chain and sourcing professionals need to reconsider “business as usual” and take this as a forewarning of things to come.
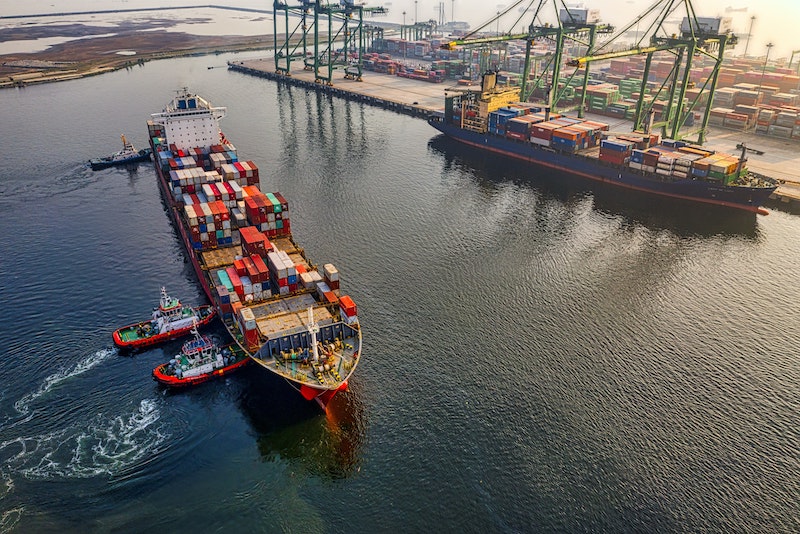
Covid-19 disruption, a boom in demand[3], labour shortage particularly of skilled workers are all interplaying with the surge in energy[4] and transportation costs[5].
The biggest sectors hit [6] are:
– Motor vehicle manufacturing
– Computer and electronics
– Rubber, metals, lumber, paper and plastics
However, this affects almost all consumer goods products including our favourite coffee[7].
The impact of lost revenue to businesses who go out-of-stock (because of not being able to sell their products to customers) will almost always have a greater impact than the price premium they would pay for sourcing from a local player or the one-off cost they would pay to approve an additional supplier. More and more, procurement’s KPI’s will shift away from only focussing on “price purchase variance” and more toward “net revenue protection”. Senior leaders should review their current KPI’s for their procurement teams to ensure that they aren’t only focused on short term savings incentives but are also focussed on longer term supply chain resilience.
With procurement professionals playing a major role in future proofing supply chains, what does the current supply chain crisis reveal to us and what tools can we use to future proof supply chains?
The first step is to “prioritize”:
If you have many steps in your supply chain and multiple items going into your products, how do you prioritize what to protect first?
Contingency planning (such as approving new suppliers, investing in new equipment, etc) takes time and money and you should have clear logic as to why you’ve chosen to invest in one part of your vulnerable supply chain and not the other. The most basic step is to do a risk or vulnerability assessment which means to matrix items or aspects by risk versus impact. If something is high impact and high risk, one should make sure to have a contingency plan there. Visual of matrix below:[8]
The second step is to create a “business contingency plan”
Now that you know what you want to protect, how do you do it?
When we think of business contingency planning, we have several actions that can be taken as part of our overarching contingency plan:
Approve multiple suppliers or equivalent grades of materials | Being single sourced with one supplier means that you are entirely exposed to their ability to supply. Common sense is to “not put all your eggs in one basket”. |
Smart product engineering | If possible, redesign product to be leaner and less reliant on high-risk materials |
Increase safety stock holding | If an item has a high shelf life, you can keep months and months of stock on hand. Of course, the upside of this is that you are at low risk of going out-of-stock but the downside is that you will have an impact on your networking capital (because you’ve bought so much stock without converting it to product to sell) and you might have storage space issues. |
Geographical diversity of suppliers with a focus on local | Don’t only approve suppliers from the same country because then should there be any country specific catastrophe or political issue, you are 100% exposed. Where feasible, choose local, even if there is a cost impact, you can start with lower allocation but at least you have an approved local supplier if international players or logistics start to have issues. |
Reduce dependency on outsourcing | Where commercially viable (cost-benefit analysis) for high-risk items and high volume, it could be worthwhile to invest in internal capabilities rather than outsourcing. |
Secure favourable contracts | Secure contracts that- Outline minimum capacity requirement- Leverage prioritization of your supply over others- Include requirement of suppliers to have a business contingency plan |
What else should procurement professionals be thinking of
– Hedging – another problem resulting from the supply chain issues is that the resultant price hikes totally destroy any budget that procurement may have put together for 2021 because the underlying commodity prices that the budget was set on are not as per reality. For volatile commodities that you buy high volumes of (e.g. oil/gas), hedging could be a good option to ensure a more consistent spend profile. Hedging is a deliberate strategy adopted to limit the potential for future losses. For example, if you buy many tonnes of palm oil, you can choose to hedge a price at which you will buy. If the price drops, you will pay more than market but if the price rises you will pay less than market so of course there is some gambling to hedging but in a highly volatile market, hedging can be a good option to ensure a flatter spend profile.
– Budgeting – Factor in inflation/CPI into next years’ plan numbers
– Leveraging our suppliers – Procurement professionals are relationship managers and can be conduits to the ideas suppliers might have about how to reduce risk. A good idea is to conduct open sessions with critical suppliers about ways you can work together to lower supplier risk.
The current supply chain shortages and disruptions are significant but likely to be transitory[9], however, there will always be risks in the supply chain and companies that plan well will win in the long term. With businesses running out of inventory to sell[10] but consumers looking to spend, being in and of stock as a business could have significant short-term impacts on revenues but also long-term impacts if market share is lost because a competitor stayed in-stock when you did not. Procurement has a big role to play in ensuring the correct areas are focussed on and supplier selection factors in risk and not only reward.
[1] Khasawneh R., Xu M (Aug 2021), Reuters, “China-US Container Shipping rates, sail past $ 20k to record”, Available at: https://www.reuters.com/business/china-us-container-shipping-rates-sail-past-20000-record-2021-08-05/, [accessed on: 24 November 2021]
[2] Domm P, (Oct 2021), CNBC, “Sharp surge in energy prices”, Available at: https://www.cnbc.com/2021/10/12/sharp-surge-in-energy-prices-threatens-economic-recovery-and-is-already-slowing-growth.html, [accessed on 24 Nov 2021]
[3] Kat G, (Oct 2021), Business Insider, “Why the supply chain is in crisis”, available at: https://www.businessinsider.com/why-store-shelves-are-empty-supply-chain-crisis-shortages-2021-10?r=US&IR=T, [accessed on: 24 Nov 2021]
[4] Domm P, (Oct 2021), CNBC, “Sharp surge in energy prices”, Available at: https://www.cnbc.com/2021/10/12/sharp-surge-in-energy-prices-threatens-economic-recovery-and-is-already-slowing-growth.html, [accessed on 24 Nov 2021]
[5] Khasawneh R., Xu M (Aug 2021), Reuters, “China-US Container Shipping rates, sail past $ 20k to record”, Available at: https://www.reuters.com/business/china-us-container-shipping-rates-sail-past-20000-record-2021-08-05/, [accessed on: 24 Nov 2021]
[6] Fisher S, (Oct 2021), IHS Markit, available at: https://ihsmarkit.com/research-analysis/supply-chain-disruptions-in-central-europe.html, [accessed on: 24 Nov 2021]
[7] Helper, S., Soltas, E., (Jun 2017), The White House, “Why the Pandemic Has Disrupted Supply Chains”, available at: https://www.whitehouse.gov/cea/blog/2021/06/17/why-the-pandemic-has-disrupted-supply-chains/ [accessed 24 Nov 2021]
[8] Research Gate, Available at: https://www.researchgate.net/figure/Qualitative-Risk-Matrix-Probability-x-Impact_fig3_275155519, [accessed 24 Nov 2021]
[9] Helper, S., Soltas, E., (Jun 2017), The White House, “Why the Pandemic Has Disrupted Supply Chains”, available at: https://www.whitehouse.gov/cea/blog/2021/06/17/why-the-pandemic-has-disrupted-supply-chains/ [accessed 24 Nov 2021]
[10] Helper, S., Soltas, E., (Jun 2017), The White House, “Why the Pandemic Has Disrupted Supply Chains”, available at: https://www.whitehouse.gov/cea/blog/2021/06/17/why-the-pandemic-has-disrupted-supply-chains/ [accessed 24 Nov 2021]